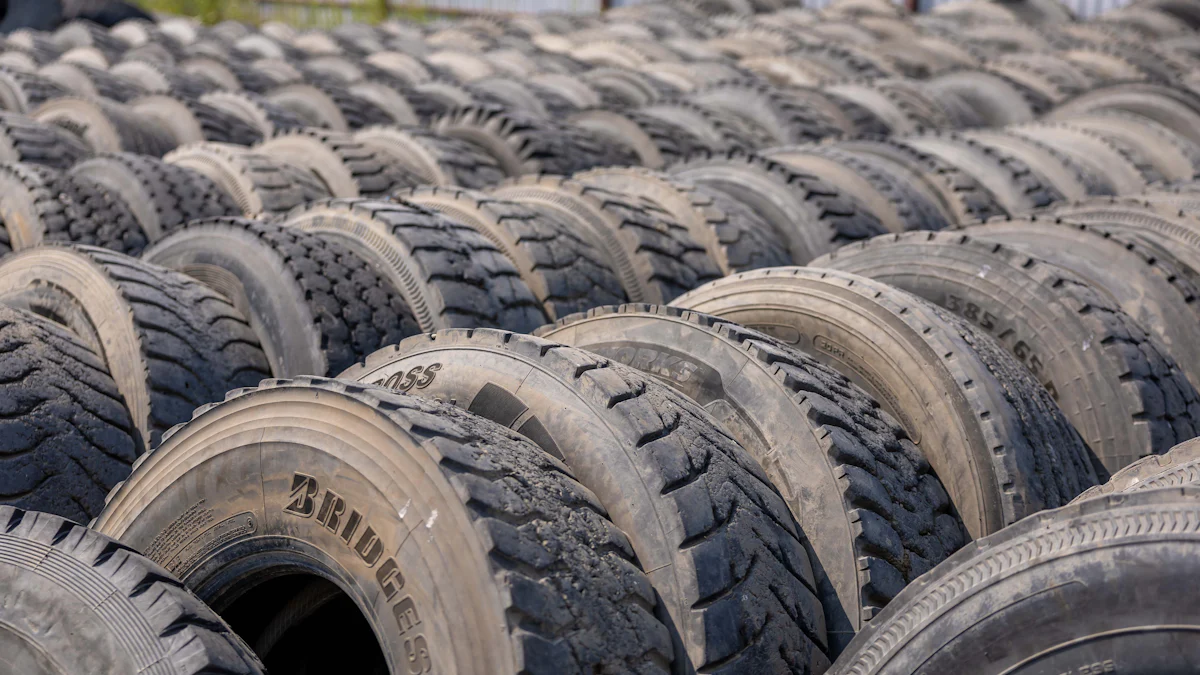
Rubber tracks for mini excavator machines endure tough conditions daily. Operators often encounter issues like cuts, cracks, and exposed wires during inspections. Debris buildup in the undercarriage can accelerate wear and lead to costly repairs. Cuts that reach steel cables may cause rust, weakening the track and risking total failure. Regular cleaning and maintenance are essential to prevent these problems. Tracks can last up to 3,000 operating hours under normal conditions, but terrain and driving habits significantly impact their lifespan. Proactive care ensures better performance and reduces downtime.
Key Takeaways
- Take care of tracks often. Check them daily for cuts, cracks, or stuck dirt to avoid expensive fixes.
- Keep track tension right. Adjust it every 10-20 hours to stop slipping and damage.
- Wash tracks after using them. Spray off dirt and mud with a pressure washer, especially after muddy jobs.
- Stay off rough ground. Don’t drive on rocks or pavement too much to protect the tracks.
- Change old tracks quickly. Watch for cracks or cords showing to stay safe and keep working well.
Premature Wear in Rubber Tracks for Mini Excavator
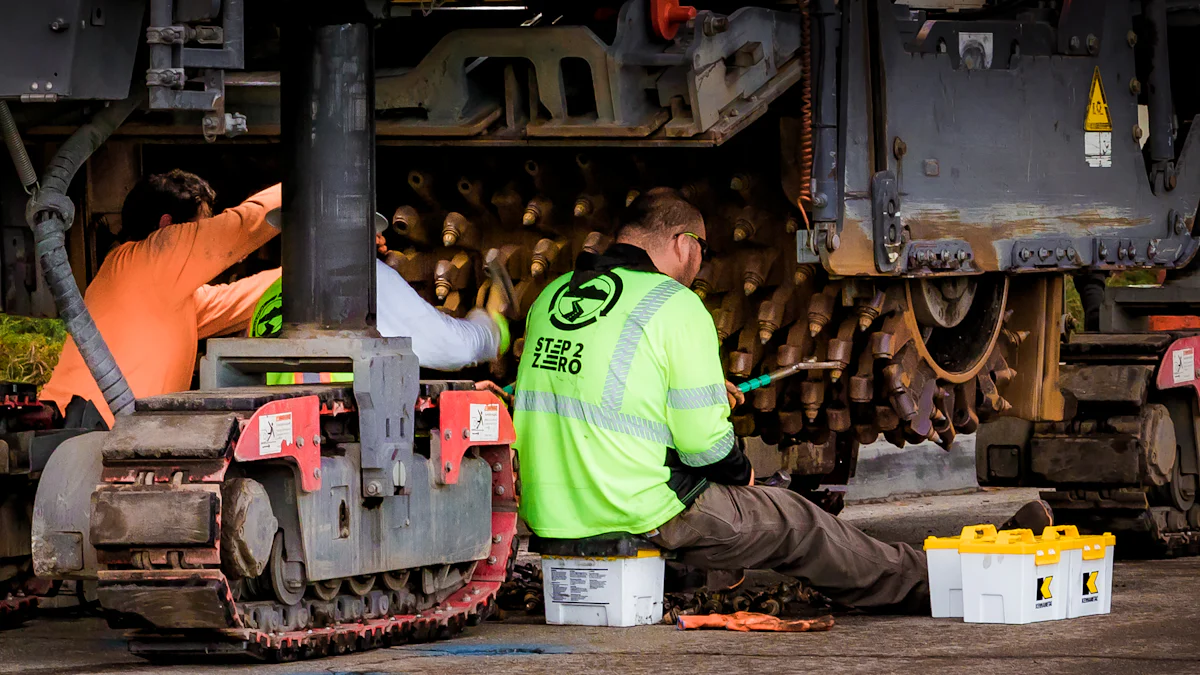
Causes of Premature Wear
Premature wear in rubber tracks for mini diggers machines often stems from several operational and environmental factors. High-speed operations generate excessive friction and heat, accelerating track degradation. Frequent reversing creates uneven wear patterns, especially on the edges of the tracks. Abrasive soil conditions, such as rocky or sandy terrains, erode the rubber faster than softer surfaces like dirt. Overloading the machine beyond its capacity also places undue stress on the tracks, leading to quicker wear. Additionally, operating on compacted surfaces increases pressure on the tracks, further reducing their lifespan.
Other factors include the distance traveled and the type of terrain. Tracks wear out faster on harsh surfaces like asphalt or rocks compared to softer ground. Poor maintenance practices, such as neglecting regular inspections or failing to clean debris, also contribute significantly to premature wear.
Solutions to Minimize Wear
Minimizing wear on mini excavator rubber tracks machines requires adopting best practices during operation and maintenance. Operators should avoid high-speed travel and limit reversing to reduce stress on the tracks. Making three-point turns instead of sharp 180-degree swings can prevent side wear. Maintaining proper track tension is crucial; check tension every 50 to 100 hours of use to ensure it remains within the recommended range.
Daily cleaning of tracks with a pressure washer removes debris that could cause damage. Replacing worn undercarriage parts promptly prevents further wear. Rotating tracks periodically ensures even tread wear, while storing the machine in a shaded or covered area protects the rubber from sunlight and ozone cracking. For long-term storage, keep tracks in a cool, dry place to maintain their flexibility.
Maintenance Tips for Longevity
Regular maintenance is key to extending the lifespan of rubber tracks. Perform daily inspections to identify cuts, cracks, or embedded debris. Check track tension after every 10-20 hours of operation and adjust as needed. Inspect drive wheels, guide wheels, and the drive shaft for signs of wear or damage. Lubricate moving parts regularly to minimize friction and prevent overheating.
Cleaning tracks after each use is essential, especially when working in muddy or clay-heavy environments. Hardened clay can over-tension the tracks, causing stress on the drive motors. By following these maintenance practices, operators can maximize the lifespan of their tracks, which can last up to 3,000 operating hours under normal conditions.
Misalignment of Rubber Tracks for Mini Excavator
Signs of Misalignment
Misalignment in rubber tracks for mini excavators can lead to significant performance issues if not addressed promptly. I always recommend looking for these common signs during routine inspections:
Sign of Misalignment | Description |
---|---|
Uneven Wear | Caused by misaligned sprockets or wheels, excessive turning, or rough terrain. Leads to loss of tension and premature failure. |
Loss of Tension | Indicates stretching or internal damage. Frequent adjustments needed suggest it’s time for new tracks. |
Excessive Vibration | Caused by misaligned sprockets, worn-out tracks, or damaged bearings. Requires inspection and possible replacement. |
If you notice any of these signs, act quickly to prevent further damage.
Common Causes of Misalignment
Several factors contribute to track misalignment. Based on my experience, these are the most common causes:
- Insufficient track spring tension
- Leaking track adjusters
- Worn undercarriage components
- Incorrectly fitted tracks
- Operator abuse, such as sharp turns or overloading
- Harsh operating conditions
- Faulty or low-quality tracks
Understanding these causes helps operators take preventive measures and avoid costly repairs.
Fixing and Preventing Misalignment
Fixing misalignment requires a systematic approach. I always start by examining the track tension and alignment. Refer to the machine’s manual for specific alignment guidelines. Regular inspections are crucial. Ensure the machine is on level ground and remove debris from roller frames to prevent irregular wear. Check for unusual wear on drive sprockets, as this often indicates misalignment.
For a more precise adjustment, follow these steps:
- Drive the machine on a smooth, straight path at near maximum speed for about 1/4 mile.
- Stop and measure the temperature of the inboard and outboard surfaces of the guide/drive lugs.
- If the temperature difference exceeds 15°F, adjust the undercarriage alignment.
- Repeat the process until the track is centered and temperatures are within 15°F.
By following these steps and maintaining proper alignment, you can extend the lifespan of your rubber tracks for mini digger machines and improve their performance.
Damage from Debris
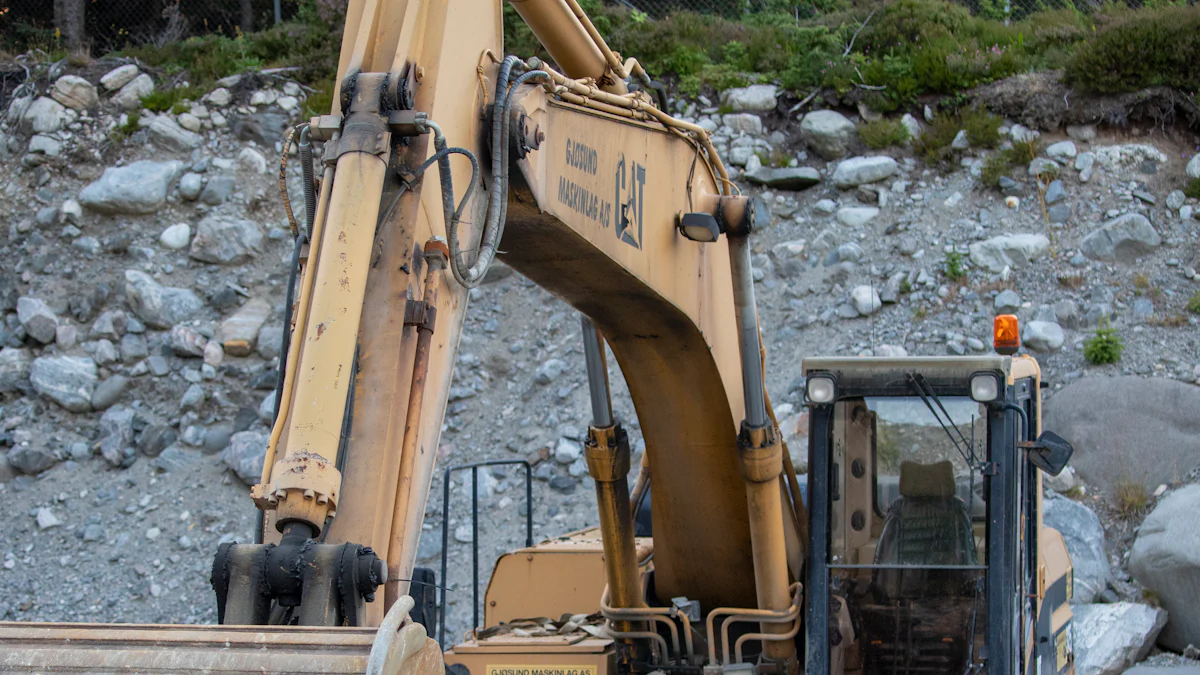
Types of Debris Damage
Debris on worksites poses a significant threat to rubber tracks for mini excavator machines. I’ve seen how certain types of debris can cause severe damage if left unchecked. Common culprits include:
- Scrap wood and cinder blocks, which can puncture or tear the rubber.
- Bricks and stones, often responsible for abrasions and cuts.
- Rebar and other sharp objects, which can slice through the rubber and expose internal components.
Impact damage from these materials weakens the track structure, leading to premature failure. Embedded debris can also create uneven wear, reducing the track’s lifespan. Operators must remain vigilant to avoid these hazards.
Preventing Damage from Debris
Preventing debris damage starts with maintaining a clean worksite. I always recommend walking the site regularly to remove hazardous materials like scrap wood, stones, and rebar. Driving carefully is equally important. Avoid sharp objects that could slice the rubber or cause impact damage.
To minimize wear, I advise limiting travel on paved or rocky surfaces. These terrains often lead to abrasions and cuts. Sharp turns should also be avoided, as they place unnecessary stress on the tracks. Contaminants like chemicals and oil can deteriorate the rubber, so keeping the worksite free of these substances is crucial. By following these practices, operators can significantly reduce the risk of debris-related damage.
Cleaning and Repairing Tracks
Cleaning and repairing mini digger tracks after exposure to debris is essential for maintaining their performance. I always use a pressure washer to remove dirt and debris at the end of each use. Embedded objects, such as stones or wood fragments, should be removed immediately to prevent further damage.
In colder climates, clearing out snow and ice is critical to avoid frozen tracks. Regular inspections of the undercarriage components help identify potential issues early. If damage occurs, repairing it promptly can prevent more extensive problems. These steps ensure that rubber tracks for mini excavator machines remain in optimal condition, even in challenging environments.
Loss of Traction in Rubber Tracks for Mini Excavator
Causes of Traction Loss
Traction loss in rubber tracks for mini excavator machines can significantly impact performance and safety. I’ve observed that several factors contribute to this issue:
- Damage from cutting or chunking exposes internal cables, reducing traction.
- Impact damage from debris weakens the rubber, leading to instability.
- Improper undercarriage maintenance causes excessive wear, affecting grip.
- Incorrect track tension results in premature failure and traction loss.
- Worn-out tracks with less pronounced lugs and treads reduce grip and stability.
- Slipping or sliding during operation often indicates traction issues.
These problems not only compromise efficiency but also increase safety risks, such as instability and potential tipping.
Solutions to Improve Traction
Improving traction starts with choosing the right tracks. Rubber tracks provide versatility, enhancing grip on various surfaces like mud, sand, and gravel. This adaptability is essential for mini excavators operating in challenging terrains. Enhanced traction ensures safer and more efficient operation, especially on soft or uneven surfaces.
Regular maintenance also plays a critical role. I recommend inspecting tracks daily for wear or damage. Adjusting track tension to the manufacturer’s specifications prevents slippage. Replacing worn tracks promptly restores optimal performance. Keeping the undercarriage clean and free of debris minimizes wear and improves traction.
Operator Techniques for Better Traction
Operators can adopt specific techniques to maintain better traction. I always advise minimizing travel on hills to reduce wear on track components. Avoid traveling sideways, as this can lead to de-tracking. When back dragging, keep the full length of the track on the ground for optimal grip.
Gradual turns are better than sharp ones, which cause side wear. Maintaining a slow ground speed reduces stress on the tracks. On sloped terrain, follow operating instructions to enhance traction. Avoid counter-rotating turns; instead, use gradual, three-point turns to preserve track integrity.
By combining proper maintenance with these techniques, operators can maximize the performance and lifespan of their rubber tracks for mini excavator machines.
Maintenance Practices for Rubber Tracks for Mini Excavator
Daily Maintenance Checklist
Daily maintenance ensures the longevity and performance of rubber tracks. I always recommend starting each day with a thorough inspection. Look for visible cuts, cracks, or exposed wires that could compromise the track’s integrity. Check for embedded debris, such as stones or metal, which can cause damage over time.
After the inspection, rinse the tracks and undercarriage with a pressure washer to remove dirt and debris. This step prevents buildup that could lead to misalignment or premature wear. Pay close attention to areas where mud or clay tends to accumulate. Keeping the tracks clean reduces stress on the undercarriage components and improves overall efficiency.
Tip: A clean and well-maintained track not only lasts longer but also enhances the machine’s performance on challenging terrains.
Long-Term Maintenance Tips
Long-term maintenance practices play a crucial role in extending the lifespan of rubber tracks for mini excavator machines. I always emphasize the importance of proper track tension. Check the tension weekly and adjust it according to the manufacturer’s guidelines. Tracks that are too tight can tear, while loose tracks can damage the cleats.
Store tracks in a cool, dry place when not in use. Avoid direct sunlight, as UV rays can cause the rubber to crack. Rotate the tracks periodically to ensure even wear. Regularly inspect and clean the undercarriage components, such as sprockets and rollers, to prevent damage.
Note: Avoid exposing tracks to chemicals or oil, as these substances can deteriorate the rubber. Following these tips can significantly reduce replacement costs and downtime.
When to Replace Rubber Tracks
Knowing when to replace rubber tracks is essential for maintaining safety and efficiency. I always look for these key indicators:
- Visible cracks or missing pieces in the rubber.
- Worn tread patterns that reduce traction.
- Exposed or frayed cords, which weaken the track’s structure.
- Signs of de-lamination, such as bubbles or peeling rubber.
- Excessive wear on sprockets or undercarriage components.
- Frequent loss of tension, indicating internal damage.
- Reduced performance, such as slower operation or higher fuel consumption.
Replacing worn tracks promptly prevents further damage to the machine and ensures optimal performance. While the cost of replacement tracks may seem high, regular maintenance can delay this expense and maximize the value of your investment.
Reminder: On average, rubber tracks last around 2,500 to 3,000 hours under normal conditions. However, harsh terrains and improper use can shorten their lifespan.
Mini excavator rubber tracks face challenges like wear, misalignment, and debris damage. However, proper care can significantly extend their lifespan and enhance performance. Regular maintenance, such as cleaning, tension adjustments, and inspections, prevents severe faults and reduces downtime. Operators should avoid common mistakes like zero-radius turns and neglecting undercarriage components, which lead to premature wear.
Proactive practices save costs by minimizing repairs and maximizing track life. Conducting daily checks, managing loads, and adapting to terrain ensure optimal performance. By following these steps, operators can maintain the reliability and efficiency of rubber tracks for mini excavator machines.
FAQ
What is the average lifespan of rubber tracks for mini excavators?
Rubber tracks typically last between 2,500 and 3,000 operating hours under normal conditions. However, harsh terrains, improper maintenance, and aggressive driving habits can shorten their lifespan. Regular inspections and proper care help maximize their durability.
How do I know when to replace my rubber excavator tracks?
Look for visible signs like cracks, missing rubber pieces, or exposed cords. Worn tread patterns and frequent loss of tension also indicate replacement is necessary. Reduced performance, such as slipping or slower operation, is another key sign.
Can I repair damaged rubber tracks, or should I replace them?
Minor damage, like small cuts or embedded debris, can often be repaired. However, significant issues like exposed steel cords, de-lamination, or severe wear require replacement. Prompt repairs prevent further damage and extend track life.
How often should I check track tension?
I recommend checking track tension every 10-20 hours of operation. Proper tension prevents slippage and reduces wear. Always follow the manufacturer’s guidelines for adjustments to ensure optimal performance and safety.
What terrains are best suited for rubber tracks?
Rubber tracks perform well on soft surfaces like dirt, mud, and sand. They also handle uneven terrains effectively. Avoid prolonged use on rocky or paved surfaces, as these can accelerate wear and damage the rubber.
Post time: Jan-09-2025