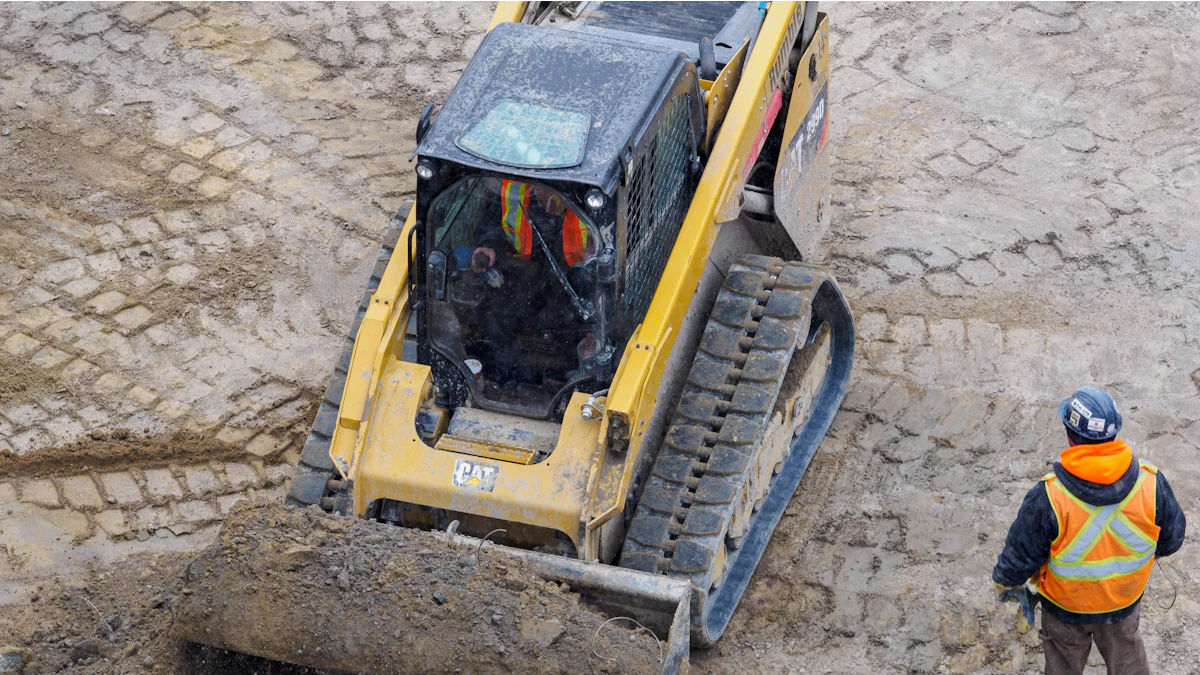
Choosing the right skid steer rubber tracks ensures optimal performance and prevents costly damage. Incompatible tracks often lead to safety hazards and equipment failure. For example:
Damage Type | Cause | Result |
---|---|---|
Corrosion of embeds | Salty or acidic terrains | Complete track separation |
Cuts on lug side | Sharp stones or projections | Steel cord breakage |
Cracks around the root of lug | Stress during operation | Full track replacement |
To avoid these issues:
- Wash tracks after exposure to corrosive environments.
- Repair cuts promptly using cold vulcanization rubber.
- Drive cautiously on rough terrains to minimize stress.
Key Takeaways
- Choosing the right skid steer rubber tracks is crucial for optimal performance and safety, preventing costly damage and equipment failure.
- Ensure compatibility with your skid steer loader by following manufacturer specifications, including track width, tread patterns, and material quality.
- Regular maintenance, including inspections and cleaning, is essential to extend the lifespan of rubber tracks and maintain their performance.
- Select tracks based on the terrain you’ll be working on; wider tracks with aggressive treads are best for muddy conditions, while narrower, reinforced tracks excel on rocky surfaces.
- Investing in high-quality rubber tracks can save money in the long run by reducing replacement frequency and enhancing overall efficiency.
Compatibility with Your Skid Steer Loader
Manufacturer Specifications
Selecting skid steer rubber tracks that align with manufacturer specifications ensures optimal performance and safety. Manufacturers often provide detailed guidelines to help users choose the right tracks. Key specifications include:
Specification | Description |
---|---|
Track Width | Wider tracks provide better stability and reduce ground pressure. |
Tread Patterns | Different patterns are suited for various applications and terrains. |
Terrain Compatibility | Tracks must match the specific terrains, such as muddy or rocky surfaces. |
Material Quality | High-grade rubber compounds ensure durability and performance. |
Reinforcement Features | Steel cords and reinforced sidewalls enhance durability and strength. |
Tracks designed with high-grade rubber compounds offer durability and resistance to wear. Reinforcement features, such as steel cords, improve strength and longevity. Matching these specifications with your skid steer loader model ensures compatibility and efficiency.
Proper Fit and Size
Properly fitting tracks are essential for safe and efficient operation. To determine the correct size:
- Width: Measure the track’s width in millimeters. For example, a width of 320 mm is written as “320.”
- Pitch: Measure the distance between the centers of two consecutive drive links in millimeters. For instance, a pitch of 86 mm is written as “86.”
- Number of Links: Count the total number of drive links around the track. For example, 52 links are written as “52.”
Some manufacturers follow OEM (Original Equipment Manufacturer) specifications, ensuring a guaranteed match with your skid steer loader. Tracks that meet OEM standards provide a precise fit, reducing the risk of operational issues.
Rubber Tracks vs. Steel Tracks
Rubber tracks offer several advantages over steel tracks for skid steer loaders:
Advantage | Description |
---|---|
Versatility | Rubber tracks can perform on many surfaces where steel tracks cannot. |
Affordability | Initial costs for rubber tracks are lower than for steel tracks. |
Comfort | Rubber tracks reduce vibrations and shock transfer, enhancing operator comfort. |
Impact | Rubber tracks have less impact on surfaces, making them ideal for sensitive areas. |
Speed | Rubber-tracked machines can move faster than those with steel tracks. |
Maneuverability | Rubber tracks offer better maneuverability, reducing damage when turning quickly. |
Rubber tracks also minimize environmental impact by reducing ground pressure and preserving soil structure. Steel tracks, while durable, can cause significant surface damage and are less suitable for delicate terrains. For most applications, rubber tracks provide a cost-effective and versatile solution.
Durability of Skid Steer Rubber Tracks
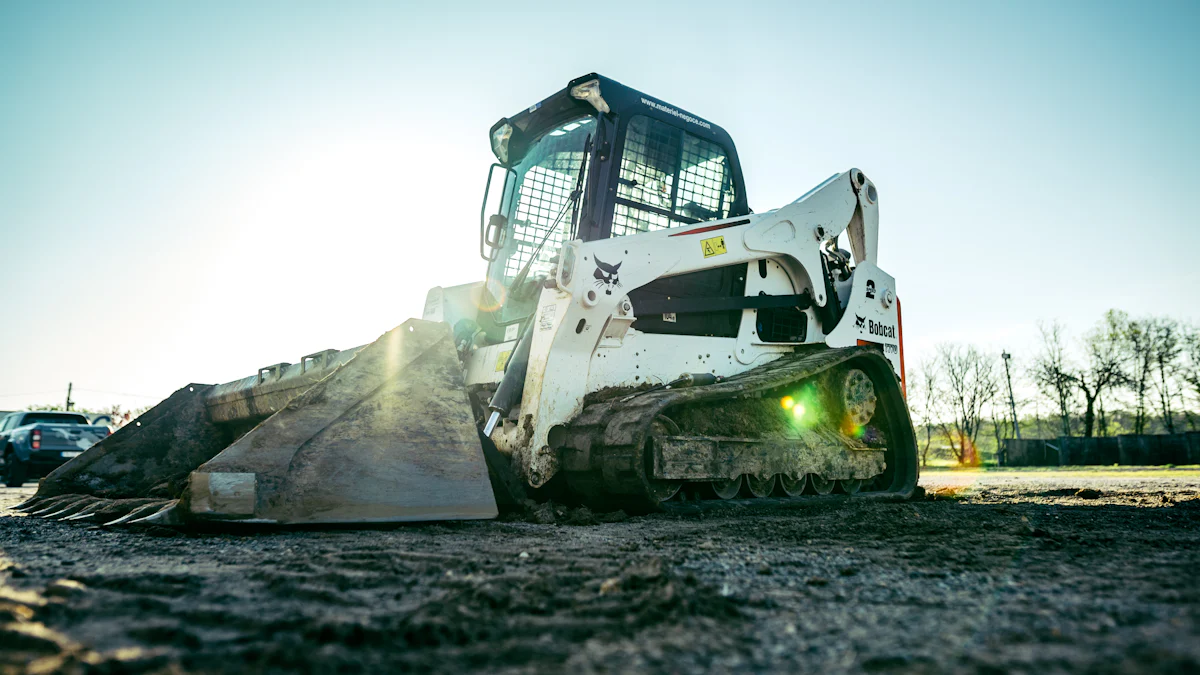
High-Quality Materials
Durability begins with the materials used in manufacturing skid loader tracks. High-grade rubber compounds provide exceptional tensile strength, abrasion resistance, and heat resistance. Synthetic rubber compounds, such as EPDM and SBR, excel in wear and weather resistance, making them ideal for demanding environments. Natural rubber blends offer flexibility and strength, which are particularly useful for softer terrains.
Reinforcement features, such as steel cords and Kevlar, further enhance durability. Steel cords improve structural integrity, while Kevlar adds resistance to cuts and punctures. These materials ensure the tracks can withstand the stresses of heavy-duty applications, extending their lifespan significantly.
Reinforcement Layers
Reinforcement layers play a critical role in improving the durability of skid steer rubber tracks. Tracks with Kevlar integration resist cuts and punctures, making them suitable for rugged job sites. Steel cords embedded within the rubber enhance tensile strength and prevent elongation under heavy loads. This feature ensures the tracks maintain their shape and effectiveness over time.
Reinforced sidewalls protect against abrasions, cuts, and punctures. They also prevent deformation, which can lead to premature failure. These layers provide additional strength, making the tracks resilient to the daily demands of construction, forestry, and other heavy-duty applications.
Resistance to Wear and Tear
Wear and tear are inevitable in skid steer rubber tracks, but understanding the causes can help minimize damage. Common issues include corrosion of embeds caused by salty or acidic terrains, cuts on the lug side from sharp objects, and small cracks around the root of the lug due to operational stress.
Proper maintenance can significantly reduce wear. Maintaining correct belt tension prevents excessive strain on the tracks. Cleaning undercarriages regularly helps identify potential problems and reduces debris-related wear. These practices ensure the tracks remain functional and durable, even in challenging conditions.
Regular inspections and timely repairs are essential for extending the lifespan of skid steer loader rubber tracks.
Terrain Suitability
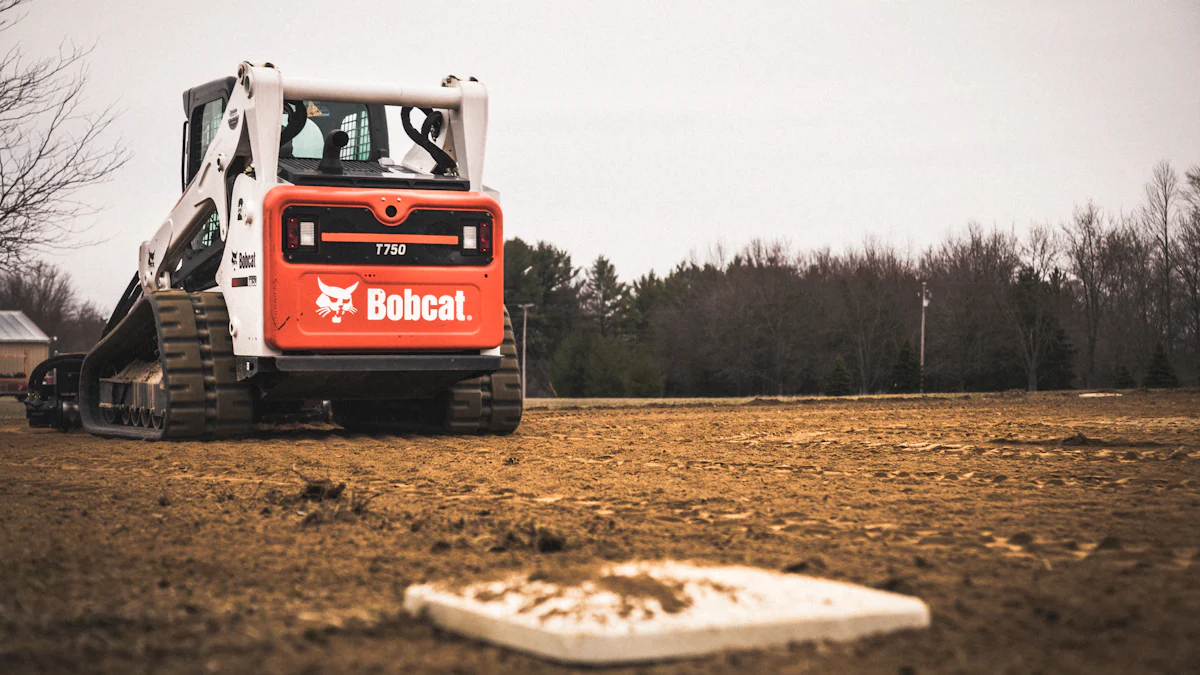
Tracks for Soft and Muddy Terrain
Soft and muddy terrains demand rubber tracks that provide superior traction and flotation. Wider tracks with aggressive tread patterns perform best in these conditions. They distribute the machine’s weight evenly, preventing it from sinking into the ground.
Several tread patterns excel in muddy environments:
- Straight Bar: Slimmer pads offer excellent traction and a smooth ride, making them ideal for wet surfaces.
- Multi-Bar Lug: Two rows of slim pads enhance traction and durability, suitable for dirt and sand but less effective on rocky terrain.
- Standard C-Pattern: C-shaped pads provide a balance of traction and durability, performing well in mud and dirt.
- Premium C-Pattern: Larger C-shaped pads deliver exceptional traction across mud, dirt, and rocky surfaces.
Operators working in muddy or snowy conditions should prioritize tracks with these features to ensure optimal performance and safety.
Tracks for Hard and Rocky Terrain
Rocky terrains require tracks designed for durability and grip. These tracks must withstand abrasive surfaces and provide stability on uneven ground. Narrower tracks with reinforced sidewalls and steel cords are ideal for such environments.
Key features of tracks for rocky terrain include:
- Enhanced durability to resist cuts, tears, and punctures.
- Superior grip to maintain stability on gravel and rocky surfaces.
- Reinforced construction to handle the stress of heavy loads.
Tracks built for rocky conditions often incorporate high-grade rubber compounds and steel reinforcements. These materials ensure the tracks endure the challenges of abrasive terrains while maintaining performance.
Versatile Tracks for Mixed Terrain
Mixed terrains require rubber tracks that balance durability, traction, and adaptability. Tracks with proprietary designs and advanced materials excel in these conditions.
Features of versatile tracks include:
- Steel-reinforced belts for added strength and resistance to high-torque loads.
- High-grade rubber compounds for durability and wear resistance.
- Enhanced rigidity to prevent de-tracking on uneven surfaces.
- Puncture and tear resistance to minimize downtime.
- Protection against delamination in tread and rolling areas.
These tracks perform well across various terrains, including mud, gravel, and rocky surfaces. Their ability to handle diverse conditions makes them a cost-effective choice for operators who frequently switch between job sites.
Tip: Regular maintenance, such as cleaning and inspecting tracks, ensures they remain effective and prolongs their lifespan.
Cost and Value Considerations
Initial Purchase Cost
The initial cost of skid steer loader tracks varies significantly based on size, quality, and application. Smaller tracks for compact loaders typically cost between 85 and 1,700 per track. Larger tracks designed for agricultural or heavy-duty use can range from 2,500 to 5,000 for a complete set. Operators should consider their specific needs when budgeting for new tracks. For example, compact tracks may suffice for light-duty tasks, while premium options are better suited for demanding environments.
Choosing cost-effective brands like Arisun or Global Track Warehouse can help balance affordability and durability. These manufacturers design tracks compatible with major skid steer brands, ensuring a reliable fit and long-lasting performance. Investing in quality tracks upfront reduces the risk of frequent replacements, saving money over time.
Long-Term Cost Efficiency
Rubber tracks offer lower initial costs compared to steel tracks, but their long-term efficiency depends on the operating environment. In harsh conditions with sharp debris, rubber tracks may require more frequent replacements, increasing overall expenses. Steel tracks, while more expensive initially, provide greater durability and a longer lifespan. This makes them a cost-effective choice for operators working in abrasive terrains.
Rubber tracks excel in environments where minimal surface damage is essential. They reduce maintenance costs for sensitive areas like lawns or paved surfaces. However, operators should weigh the potential for higher replacement costs against the benefits of reduced ground pressure and versatility.
Balancing Budget and Quality
Balancing budget and quality requires careful consideration of terrain, performance, and supplier reputation. Tracks designed for specific terrains, such as mud or rocky surfaces, enhance efficiency and reduce wear. High-quality materials like reinforced rubber and steel cords ensure durability, minimizing downtime and replacement costs.
Operators should determine their budget and evaluate the return on investment (ROI) for premium tracks. Investing in high-grade tracks often results in better performance and reduced maintenance. For those with limited budgets, economy tracks may suffice for infrequent use or short-term projects. Reputable suppliers like Arisun and Global Track Warehouse provide reliable options that meet various budgetary needs.
Tip: Prioritize tracks that match your skid steer loader’s specifications and intended use to maximize value and performance.
Maintenance and Care
Regular Inspections
Routine inspections are essential for maintaining skid steer rubber tracks and ensuring their longevity. Operators should check the undercarriage regularly to identify potential issues early. Daily inspections of track tension and condition help prevent excessive wear and operational failures. Visual checks for damage, such as cracks, missing chunks, or exposed cords, are crucial. Lubricating grease points during these inspections reduces friction and extends component life.
Signs of wear, misalignment, or damage should be addressed promptly. Routine adjustments and repairs prevent minor issues from escalating into costly replacements. Regular inspections also minimize downtime, ensuring the equipment remains operational and efficient.
Tip: Conduct inspections every 50 to 100 hours to maintain optimal track performance and reduce the risk of de-tracking.
Cleaning and Storage
Proper cleaning and storage practices significantly impact the lifespan of skid steer rubber tracks. Operators should clean tracks and undercarriages regularly to remove dirt, debris, and other contaminants. After working in wet or muddy conditions, thorough cleaning prevents long-term damage caused by moisture and mud accumulation. Every 200 hours, removing the track and performing a deep cleaning ensures all components remain in good condition.
When storing tracks, place them in a cool, dry environment away from direct sunlight. Elevating the tracks off the ground prevents flat spots from forming and reduces the risk of deformation. These practices help maintain the structural integrity of the tracks and ensure they are ready for use when needed.
Note: Keeping tracks clean and properly stored reduces wear and extends their service life.
Repair and Replacement
Timely repairs and replacements are critical for maintaining the safety and efficiency of skid steer rubber tracks. Operators should replace worn or damaged sprockets and wheels to prevent further track damage. External signs such as cracks, missing lugs, or exposed cords indicate the need for immediate attention. Irregular tread depth or unsafe tension levels can compromise traction and stability, requiring adjustments or replacements.
Routine maintenance schedules help identify issues early, reducing the likelihood of unexpected failures. Proper tension levels prevent excessive wear and de-tracking. Avoiding harsh surfaces and overloading the equipment minimizes the risk of cuts and punctures.
Alert: Ignoring signs of wear, such as unusual noises or frequent adjustments, can lead to costly repairs and unsafe operating conditions.
Choosing the best skid steer rubber tracks requires evaluating several factors, including compatibility, durability, terrain suitability, cost, and maintenance. Operators should prioritize quality and consult their skid steer loader’s manual to ensure the tracks meet manufacturer specifications. Durable tracks enhance stability, reduce ground compaction, and improve productivity, making them a worthwhile investment.
Use this checklist to guide your decision:
- Are the tracks compatible with your skid steer loader?
- Do they suit the terrain you’ll be working on?
- Are they durable and cost-effective in the long term?
- Are you prepared to maintain them properly?
Tip: Regular inspections, proper cleaning, and correct storage practices extend the lifespan of rubber tracks and maximize their performance.
FAQ
What are the benefits of using rubber tracks over tires?
Rubber tracks provide better traction, reduced ground pressure, and improved stability. They perform well on soft or uneven terrains and minimize surface damage. Tracks also enhance operator comfort by reducing vibrations compared to tires.
How often should skid steer rubber tracks be replaced?
Replacement depends on usage and terrain. On average, rubber tracks last 1,200 to 1,600 hours. Regular inspections and proper maintenance extend their lifespan. Operators should replace tracks showing significant wear, cracks, or exposed cords.
Can rubber tracks be repaired instead of replaced?
Minor damage, such as small cuts or punctures, can be repaired using cold vulcanization rubber. However, severe damage like exposed steel cords or large tears requires replacement to ensure safety and performance.
How do I choose the right tread pattern for my application?
Select tread patterns based on terrain. Straight bar patterns suit muddy conditions, while C-patterns work well on mixed terrains. For rocky surfaces, choose reinforced tracks with durable tread designs for better grip and longevity.
What factors affect the cost of skid steer rubber tracks?
Track size, material quality, and application influence cost. Smaller tracks for compact loaders are more affordable, while heavy-duty tracks for agricultural use cost more. Investing in high-quality tracks reduces long-term expenses by minimizing replacements.
Tip: Consult your skid steer loader’s manual to ensure compatibility when selecting tracks.
Post time: Jan-06-2025