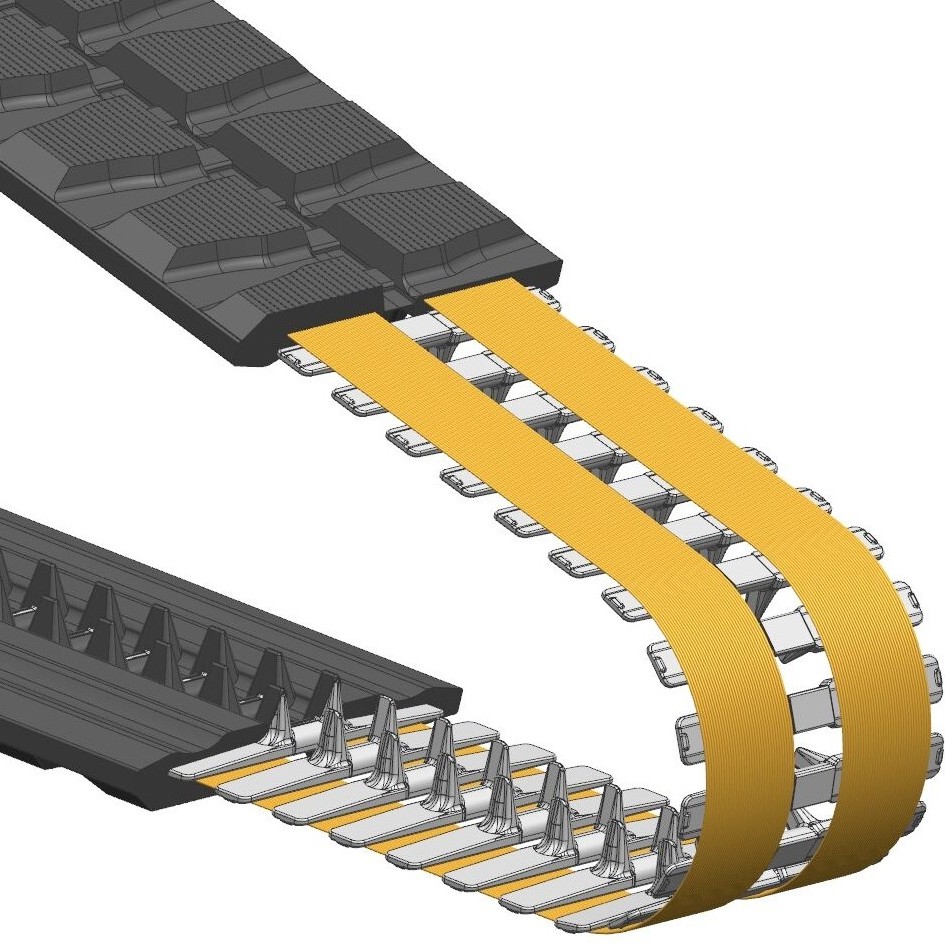
I’ve seen how operators face challenges with rubber tracks, from premature wear to debris buildup. ASV Tracks, crafted by Gator Track Co., Ltd, solve these issues with innovative engineering. For example, track damage often occurs on rough terrain, but these tracks use reinforced materials to withstand industrial demands. Regular cleaning prevents dirt accumulation, which can otherwise increase tension and wear. With features like pre-stretched designs and advanced treads, ASV Tracks deliver unmatched durability and performance. As an ASV Tracks manufacturer, we prioritize quality to ensure operators can rely on their equipment in any condition.
Key Takeaways
- Regular maintenance is crucial; inspect tracks for wear and ensure proper tensioning to extend their lifespan and prevent costly repairs.
- ASV Tracks are designed with advanced materials and a single-cure process, providing unmatched durability and reducing the risk of premature wear.
- Cleaning tracks after each use, especially in debris-prone environments, prevents accumulation that can lead to performance issues and increased maintenance costs.
- Utilizing the Posi-Track® undercarriage system enhances stability and traction, allowing operators to navigate challenging terrains with confidence.
- Investing in high-quality ASV Tracks not only improves operational efficiency but also reduces downtime and long-term costs associated with track replacements.
Common Problems with Rubber Tracks
Premature Wear
Premature wear is one of the most common issues I’ve encountered with rubber tracks. It often stems from several factors that operators might overlook:
- Excessive machine weight creates high ground pressure, accelerating wear.
- Aggressive operation, such as counter-rotations, increases stress on the tracks.
- Driving over abrasive materials like granite or shale causes rapid degradation.
- Inadequate maintenance, including improper cleaning, reduces the track’s lifespan.
- Incorrect tensioning leads to uneven pressure, which wears out the tracks faster.
I’ve also noticed that side wear and debris ingestion can damage the guide and drive lugs. When the carcass gets exposed, the tracks become unserviceable. To combat these issues, I always recommend using tracks designed for durability, like ASV Tracks, which are pre-stretched and built to handle industrial demands.
Tip: Regularly inspect your tracks for signs of wear and ensure proper tensioning to extend their lifespan.
Uneven Wear
Uneven wear significantly impacts the performance and lifespan of rubber tracks. I’ve seen this issue arise from bent undercarriage mounting frames or worn undercarriage parts. These problems cause the track to shift, leading to uneven stress distribution.
- Increased stress accelerates wear and creates vibrations during operation.
- Over time, this can damage the hydraulic drive system, resulting in costly repairs.
To prevent uneven wear, I always advise operators to check their undercarriage components regularly. Tracks like ASV Rubber Tracks, with their advanced design and Posi-Track® undercarriage system, help minimize these risks by ensuring consistent ground contact.
Track Damage
Track damage is another challenge I’ve observed, especially in harsh working environments. Driving over sharp or abrasive materials often leads to cuts and punctures. Excessive pressure on idlers and bearings can also contribute to damage.
Note: Proper operation and avoiding aggressive maneuvers, like sudden counter-rotations, can reduce the risk of track damage.
ASV Tracks address these issues with reinforced construction and a single-cure process, ensuring they withstand industrial use. Their specialized rubber compounds provide added resilience, making them a reliable choice for demanding applications.
Debris Accumulation
Debris accumulation is a frequent issue I’ve observed with rubber tracks, especially in environments with loose soil, gravel, or vegetation. When debris builds up, it can interfere with the undercarriage system and increase wear on the tracks. This problem often leads to reduced performance and higher maintenance costs.
- Common causes of debris buildup:
- Operating in muddy or sandy conditions.
- Working in areas with excessive vegetation or rocks.
- Neglecting regular cleaning routines.
When debris gets lodged in the undercarriage, it creates additional friction. Over time, this friction can damage the track’s surface and even affect the sprockets and rollers. I’ve seen cases where operators ignored debris buildup, resulting in costly repairs and downtime.
Tip: Always clean the tracks after each use, especially when working in debris-prone environments.
ASV Tracks simplify this process with their easy-to-clean design. The pre-stretched construction ensures proper tension, reducing the likelihood of debris getting trapped. Additionally, the Posi-Track® undercarriage system maintains consistent ground contact, which helps prevent debris from accumulating in the first place. These features make ASV Tracks a reliable choice for operators who work in challenging conditions.
Maintenance Challenges
Maintenance challenges often arise when operators lack the tools or knowledge to care for their tracks properly. I’ve noticed that improper tensioning, infrequent inspections, and inadequate cleaning are the most common issues. These oversights can lead to premature wear, uneven performance, and even track failure.
- Key maintenance challenges:
- Ensuring correct track tension.
- Identifying early signs of wear or damage.
- Removing debris effectively without damaging the tracks.
Neglecting maintenance not only shortens the lifespan of the tracks but also increases the risk of equipment downtime. I always recommend following a consistent maintenance schedule to avoid these problems.
ASV Tracks address these challenges with their maintenance-friendly features. The pre-stretched design minimizes the need for frequent tension adjustments. Their durable construction reduces the likelihood of damage, even in demanding environments. Operators can also benefit from the easy-to-clean design, which simplifies debris removal and ensures optimal performance.
Note: Regular inspections and proper tensioning are essential for maximizing the lifespan of your tracks.
By investing in ASV Tracks, operators can overcome common maintenance challenges and ensure their equipment performs reliably in any condition.
How ASV Tracks Solve Rubber Track Issues
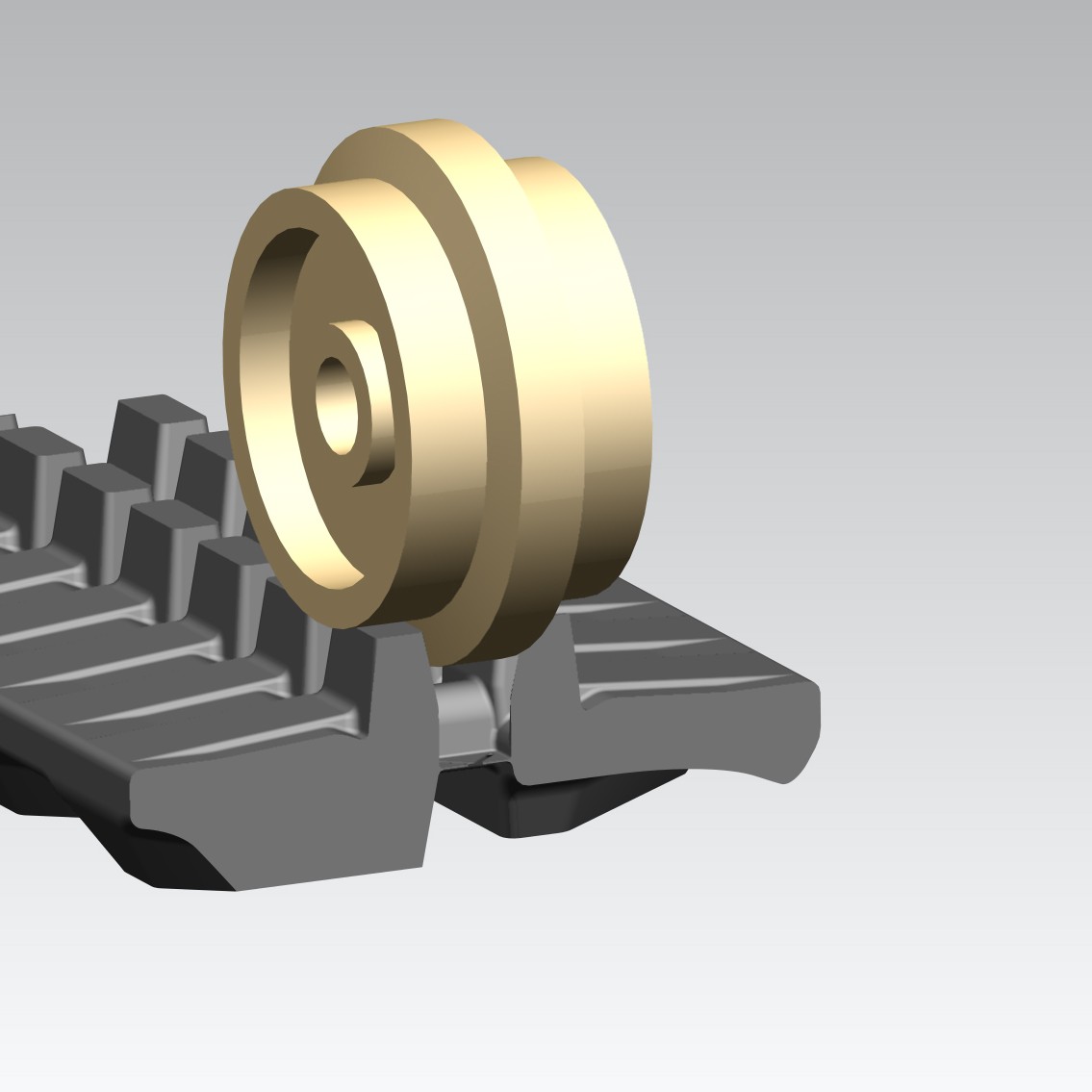
Durability and Advanced Design
High-quality materials and single-cure process
I’ve always believed that durability starts with the right materials. ASV Tracks use a rubber construction without steel cores, embedding high-tensile poly-cords to prevent stretching and derailment. This design not only enhances flexibility but also eliminates the risk of rust or breakage. The single-cure process ensures a seamless structure, free from weak points often found in aftermarket alternatives.
Additionally, these tracks feature seven layers of embedded materials that resist punctures and cuts. This layered construction maximizes durability while allowing the tracks to flex around obstacles. I’ve seen how this combination of strength and elasticity reduces wear, even in harsh environments.
- ASV Tracks withstand industrial demands due to advanced materials and processes.
- The absence of steel prevents corrosion, ensuring long-term reliability.
- A unique suspension system minimizes vibration, improving operator comfort.
Reinforced construction for industrial use
ASV Tracks are built for tough jobs. The reinforced construction handles heavy loads and abrasive surfaces with ease. I’ve noticed that operators working in rugged conditions benefit from the tracks’ ability to maintain performance without compromising longevity. This makes them an excellent choice for industrial applications.
Enhanced Traction and Stability
All-season bar-style tread pattern
Traction is critical for efficient operation. ASV Tracks utilize an all-season bar-style tread pattern that provides exceptional grip on loose soil, wet surfaces, and even slippery terrain. The specially-formulated exterior tread ensures consistent performance year-round.
Posi-Track® undercarriage system for derailment prevention
The Posi-Track® undercarriage system is a game-changer. It maximizes ground contact, virtually eliminating derailment. I’ve seen how this system enhances stability and prevents slippage, even on uneven terrain. Operators can navigate challenging environments with confidence, knowing their equipment will stay on track.
- ASV Tracks improve grip with rubber-on-rubber contact points.
- A fully suspended frame enhances ride quality and stability.
- The design ensures reliable traction in diverse conditions.
Maintenance-Friendly Features
Pre-stretched tracks for minimal stretching
Maintenance becomes easier with pre-stretched tracks. ASV Tracks maintain a consistent length, reducing the need for frequent tension adjustments. This feature minimizes wear and ensures reliable performance over time.
Easy-to-clean designs and proper tensioning systems
Cleaning ASV Loader Tracks is straightforward. Their design prevents debris from accumulating, which reduces friction and wear. I always recommend these tracks for operators who work in debris-prone environments. The proper tensioning systems further simplify maintenance, ensuring optimal performance with minimal effort.
By addressing durability, traction, and maintenance challenges, ASV Tracks set a new standard for reliability. As an ASV Tracks manufacturer, we focus on creating products that operators can trust in any condition.
Operator Training and Usage Tips
Best practices for operating ASV Tracks
I’ve learned that proper operation plays a crucial role in maximizing the performance and lifespan of ASV Tracks. Operators should always start by familiarizing themselves with the equipment’s specifications and capabilities. Understanding the weight limits and terrain compatibility ensures the tracks perform optimally without unnecessary strain.
When operating machinery equipped with ASV Tracks, I recommend maintaining a steady speed and avoiding abrupt maneuvers. Sudden stops, sharp turns, or counter-rotations can place excessive stress on the tracks, leading to premature wear. Instead, smooth and controlled movements help distribute pressure evenly across the track surface.
Another best practice involves monitoring the undercarriage system during operation. I always advise operators to check for debris buildup or misalignment, as these issues can affect performance. Regularly inspecting the tension and ensuring it remains within the recommended range also prevents unnecessary strain on the tracks.
Tip: Always consult the user manual provided by the asv tracks manufacturer for specific operational guidelines tailored to your equipment.
Tips for avoiding unnecessary wear and tear
Avoiding unnecessary wear and tear begins with proper preparation. Before starting any job, I suggest inspecting the worksite for sharp objects, large rocks, or other hazards that could damage the tracks. Clearing the area of potential threats reduces the risk of cuts or punctures.
I’ve also found that maintaining consistent track tension is essential. Tracks that are too loose can derail, while overly tight tracks increase friction and wear. Using the built-in tensioning system on ASV Tracks simplifies this process, ensuring the correct tension every time.
Another tip is to avoid prolonged operation on abrasive surfaces like asphalt or concrete. These materials accelerate wear, especially if the tracks are not designed for such conditions. If working on these surfaces is unavoidable, I recommend limiting the time spent on them and inspecting the tracks afterward.
Finally, cleaning the tracks after each use prevents debris accumulation, which can lead to uneven wear. The easy-to-clean design of ASV Tracks makes this task straightforward, saving time and effort.
Note: Following these tips not only extends the lifespan of your tracks but also enhances the overall efficiency of your machinery.
Maintenance Best Practices for ASV Tracks
Cleaning
Effective debris removal techniques
Keeping ASV Tracks clean is essential for maintaining their performance and longevity. I always recommend focusing on the undercarriage, as debris buildup can lead to unnecessary wear. Here are some effective techniques I’ve found useful:
- Use a pressure washer or a small shovel to remove mud, clay, and gravel.
- Pay special attention to the front and rear roller wheels, where debris tends to accumulate.
- Remove sharp rocks and demolition debris immediately to prevent damage.
- Clean the tracks several times a day when working in muddy or abrasive conditions.
By following these steps, operators can prevent debris from interfering with the undercarriage system and reduce the risk of track damage.
Recommended cleaning frequency
Daily cleaning is usually sufficient for most applications. However, I’ve noticed that operators working in challenging environments, such as muddy or rocky terrains, may need to clean their tracks multiple times a day. Adjusting the cleaning frequency based on the job site conditions ensures optimal performance and minimizes wear.
Tip: Consistent cleaning not only extends the lifespan of your tracks but also reduces downtime caused by maintenance issues.
Tensioning
Importance of proper track tension
Proper track tension plays a critical role in the performance of ASV Tracks. I’ve seen how loose tracks can lead to idler fractures and misfeeding, while overly tight tracks increase stress on the machine, consuming more fuel and risking bearing failure. Maintaining the correct tension ensures smooth operation and extends the lifespan of the tracks.
Steps to ensure correct tensioning
To achieve proper tensioning, I follow these steps:
- Loosen the two bolts securing the drive table to the undercarriage frame rail. Remove them if they are at the forward end of the slots.
- Adjust the tension turnbuckle to relieve pressure on the bolts.
- Extend the turnbuckle until the correct tension is achieved.
- Retighten the bolts, ensuring equal spacing in their slots for proper sprocket alignment.
Note: After the first 50 hours of operation, check the tension and make adjustments as needed.
Inspection
Regular checks for wear and damage
Regular inspections are vital for identifying potential issues early. I always advise operators to check for signs of wear, such as cracks, cuts, or exposed cords. Inspecting the undercarriage components, including sprockets and rollers, ensures everything functions correctly.
Identifying and addressing potential issues early
Spotting problems early can save time and money. For example, I’ve seen how addressing minor cuts or misalignments prevents more significant damage. Operators should also monitor the tension and alignment during inspections to avoid unnecessary strain on the tracks.
Tip: Schedule inspections weekly or after every 50 hours of operation to maintain peak performance.
By following these maintenance practices, operators can ensure their ASV Tracks deliver reliable performance in any condition.
Why Choose Gator Track Co., Ltd as Your ASV Tracks Manufacturer
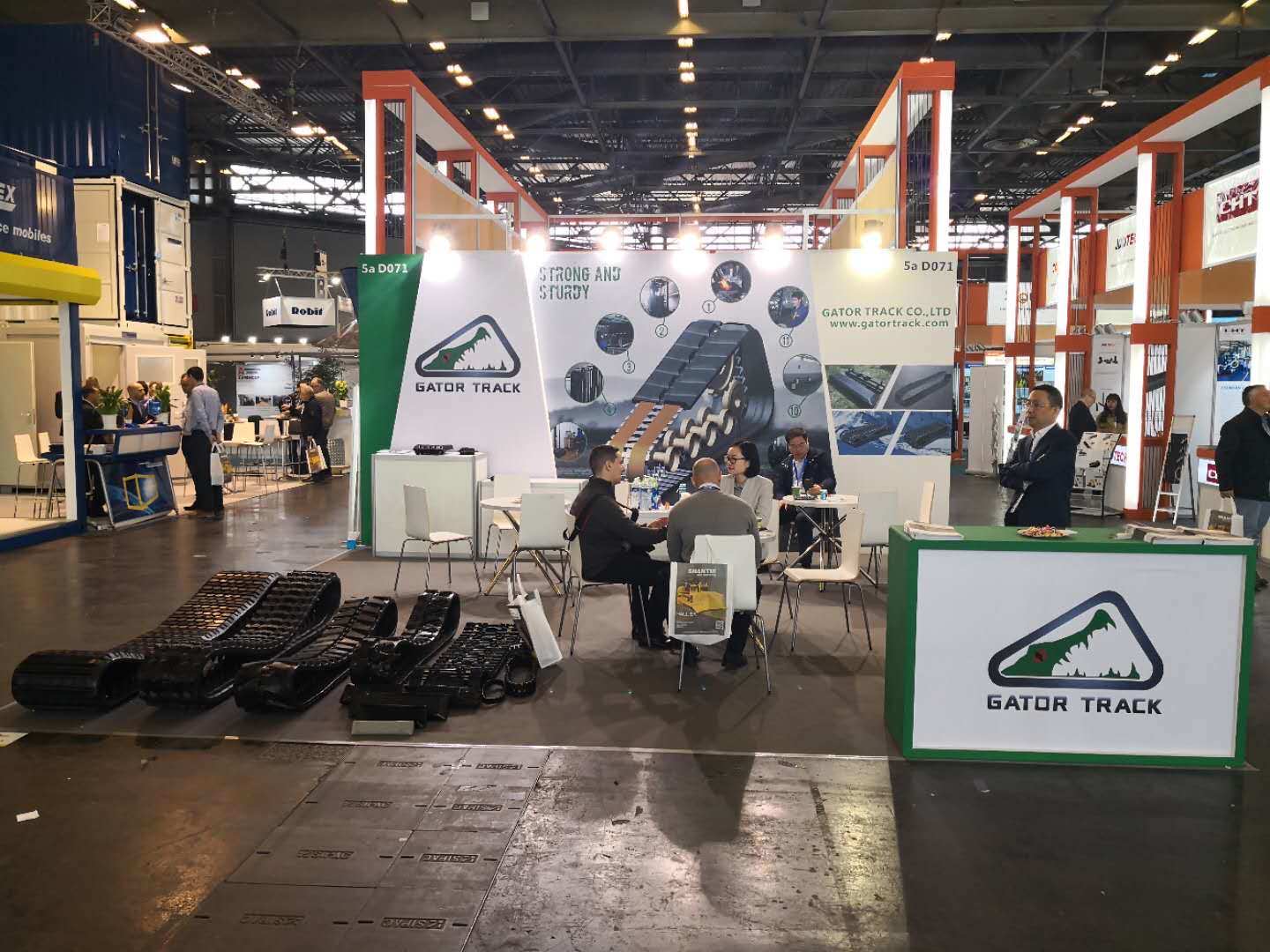
Commitment to Quality and Innovation
ISO9000-based quality control measures
I’ve always believed that quality is the foundation of any reliable product. At Gator Track Co., Ltd, we implement a rigorous quality control system based on ISO9000 standards. Every stage of production, from raw material procurement to the vulcanization process, undergoes strict monitoring. This ensures that each ASV Track meets or exceeds client expectations. By focusing on material quality and production precision, we deliver tracks that operators can trust in the most demanding conditions.
Note: Our commitment to quality ensures that every ASV Track performs optimally right from the start.
Customization options for specific machinery needs
I’ve seen how different machinery and terrains require tailored solutions. Gator Track Co., Ltd offers extensive customization options to meet these unique needs:
- Custom tread patterns designed for specific operational challenges.
- Enhanced durability for rocky or abrasive terrains.
- Improved traction and reduced ground pressure for better productivity.
- Extended track lifespan through tailored designs.
Our engineers, with over 20 years of experience, can even develop new patterns based on samples or drawings. This expertise allows us to create ASV Tracks that perfectly align with your machinery’s requirements.
Tip: Customization not only boosts performance but also reduces long-term operational costs.
Global Reputation and Expertise
Trusted partnerships with global brands
Gator Track Co., Ltd has built a strong reputation by partnering with well-known brands worldwide. I’ve seen how these collaborations reflect our reliability and commitment to excellence. Our tracks are trusted in markets across the United States, Canada, Brazil, Japan, Australia, and Europe. These partnerships highlight our ability to meet diverse industry standards and deliver consistent quality.
Over 20 years of engineering experience in rubber products
Our team’s extensive experience in rubber products sets us apart. With over two decades of expertise, we’ve mastered the art of designing innovative and durable tracks. Here’s how this experience benefits our customers:
Benefit | Description |
---|---|
Reliable Quality | Every product meets and exceeds client standards for quality. |
Innovative Designs | Our engineers develop new patterns based on their vast experience. |
Strong Commitment to Service | We prioritize “quality first, customer first,” ensuring customer satisfaction at every step. |
This depth of knowledge allows us to deliver ASV Tracks that operators can rely on, regardless of the application or environment.
Callout: When you choose Gator Track Co., Ltd, you’re not just buying a product—you’re investing in expertise, innovation, and reliability.
ASV Tracks, crafted by Gator Track Co., Ltd, solve common rubber track issues with innovative features and robust construction. Their advanced materials and single-cure process ensure unmatched durability, reducing wear and tear even in harsh environments. Operators benefit from fewer replacements and repairs, saving both time and money.
Proper maintenance practices, like regular cleaning and tension checks, further enhance the performance and lifespan of these tracks. I’ve seen how daily inspections for cuts or debris accumulation prevent unnecessary downtime. These steps ensure ASV Tracks deliver consistent reliability across various terrains and conditions.
Investing in high-quality tracks like ASV offers long-term benefits. Operators experience reduced downtime, enhanced traction, and improved operational efficiency. With their durability and versatility, ASV Tracks remain a trusted choice for demanding applications. As an experienced asv tracks manufacturer, we prioritize quality and innovation to meet the needs of operators worldwide.
FAQ
What makes ASV Tracks different from other rubber tracks?
ASV Tracks stand out due to their single-cure process, pre-stretched design, and Posi-Track® undercarriage system. These features enhance durability, prevent derailment, and reduce maintenance needs. I’ve seen how these tracks outperform aftermarket alternatives in both reliability and lifespan.
How often should I clean ASV Tracks?
I recommend cleaning ASV Tracks daily, especially after working in muddy or debris-heavy environments. For extreme conditions, such as rocky or sandy terrains, cleaning multiple times a day ensures optimal performance and prevents unnecessary wear.
Can ASV Tracks handle extreme weather conditions?
Yes, ASV Tracks perform exceptionally well in all seasons. The bar-style tread pattern and specially formulated rubber compounds provide excellent traction on wet, dry, or slippery surfaces. I’ve seen them maintain reliability in both freezing winters and scorching summers.
How do I ensure proper tensioning for ASV Tracks?
To maintain proper tension, use the built-in tensioning system. Adjust the turnbuckle until the track achieves the recommended tension. I always advise checking tension after the first 50 hours of operation and periodically during regular maintenance.
Are ASV Tracks customizable for specific machinery?
Absolutely. Gator Track Co., Ltd offers customization options, including unique tread patterns and enhanced durability for specific terrains. I’ve worked with clients to develop tailored solutions that improve performance and extend track lifespan for their machinery.
Post time: Jan-06-2025