How to Measure and Ensure Proper Fit for Rubber Digger Tracks
Steps to Measure Rubber Tracks
Accurate measurements are essential when selecting rubber tracks for excavators. Properly fitting tracks ensure optimal performance and prevent unnecessary wear. Follow these steps to measure your rubber tracks correctly:
-
1. Measure the Track Width
Use a measuring tape to determine the width of the track. Place the tape across the widest part of the track. Record the measurement in millimeters, as most manufacturers use this unit. -
2. Count the Number of Links
Inspect the track and count the total number of metal links or lugs. These links are the raised sections on the inner side of the track that engage with the sprockets. Accurate counting is crucial for compatibility. -
3. Determine the Pitch
Measure the distance between the centers of two consecutive links. This measurement, known as the pitch, is critical for ensuring the track fits your excavator’s undercarriage system. Use a ruler or tape measure for precision. -
4. Check the Overall Length
Multiply the pitch by the total number of links to calculate the overall length of the track. This step helps confirm the track size and ensures it matches your machine’s specifications. -
5. Consult the Equipment Manual
Refer to your excavator’s manual for recommended track dimensions. Compare your measurements with the manufacturer’s guidelines to verify compatibility.
By following these steps, you can confidently select tracks that fit your excavator perfectly. Accurate measurements reduce the risk of installation issues and enhance the machine’s performance.
Common Fitment Mistakes to Avoid
Improper fitment of rubber excavator tracks can lead to costly repairs and reduced efficiency. Avoid these common mistakes to ensure your tracks perform as expected:
-
Skipping Measurements
Never assume that all tracks of the same size will fit your excavator. Always measure the width, pitch, and number of links to confirm compatibility. -
Ignoring Manufacturer Guidelines
Each excavator model has specific requirements for track size and type. Ignoring these guidelines can result in poor performance or damage to the undercarriage. -
Choosing the Wrong Track Type
Selecting tracks based solely on price or appearance can lead to mismatched performance. Consider the terrain, application, and machine specifications when choosing tracks. -
Overlooking Wear and Tear
Replacing only one track instead of both can cause uneven wear. Always replace tracks in pairs to maintain balance and stability. -
Improper Installation
Incorrect installation can damage the tracks or the machine. Follow the manufacturer’s instructions or consult a professional to ensure proper fitment.
Avoiding these mistakes will save you time and money while extending the lifespan of your rubber tracks. Proper fitment enhances your excavator’s efficiency and ensures smooth operation on any job site.
Maintenance Tips to Extend the Life of Rubber Excavator Tracks
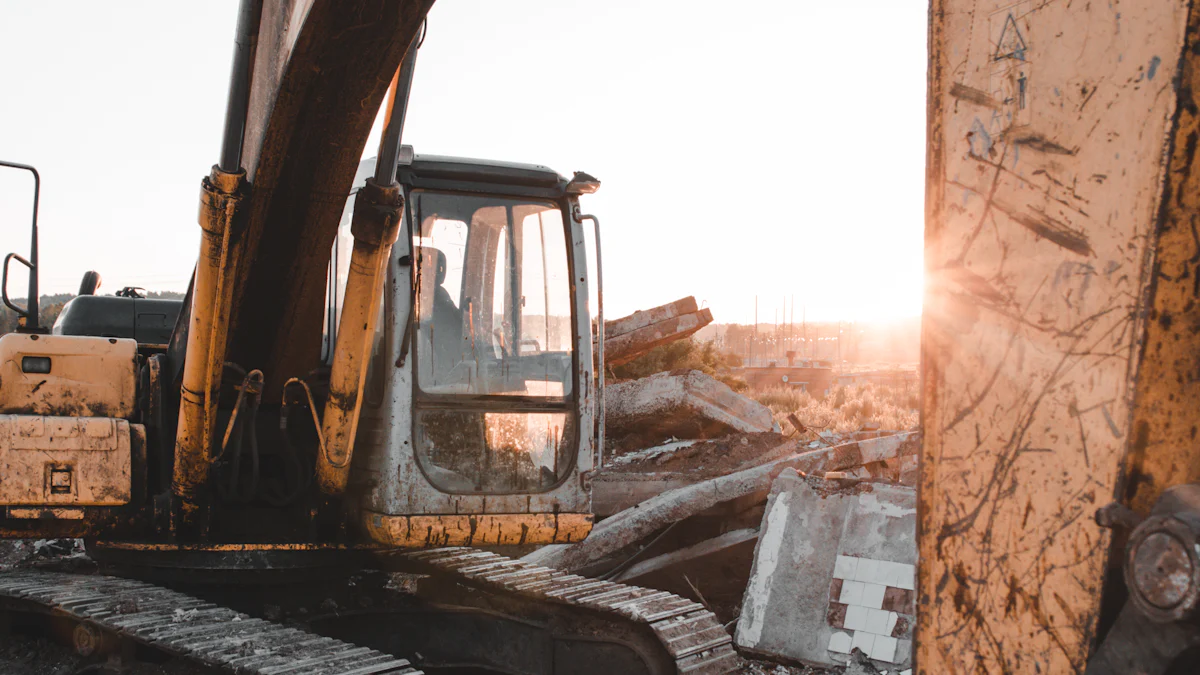
Regular Cleaning and Inspection
Keeping your rubber excavator tracks clean is essential for maintaining their performance and longevity. Dirt, debris, and rocks can get lodged in the tracks, causing unnecessary wear and tear. After each use, inspect the tracks for any buildup. Use a pressure washer or a stiff brush to remove mud, stones, and other debris. Pay close attention to the areas around the sprockets and rollers, as these spots often accumulate the most dirt.
Regular inspections help you identify potential issues before they escalate. Look for signs of damage, such as cracks, cuts, or missing lugs. Check the steel cores within the tracks for rust or corrosion. If you notice uneven wear, it could indicate a problem with the alignment or tensioning of the tracks. Addressing these issues promptly will prevent further damage and extend the life of your excavator with rubber tracks.
Proper Tensioning of Tracks
Maintaining the correct tension in your rubber digger tracks is crucial for optimal performance. Tracks that are too loose can slip off the undercarriage, while overly tight tracks can cause excessive strain on the machine. Both scenarios lead to premature wear and potential damage.
To check the tension, measure the sag in the track between the rollers. Refer to your equipment manual for the recommended sag measurement. Adjust the tension using the tensioning system provided by the manufacturer. Ensure the tracks are neither too tight nor too loose. Regularly monitor the tension, especially after heavy use or when operating on challenging terrains.
Proper tensioning not only improves the efficiency of your rubber excavator tracks but also reduces the risk of costly repairs. It ensures the tracks stay securely in place, allowing your machine to operate smoothly and safely.
Storage and Usage Best Practices
How you store and use your rubber excavator tracks significantly impacts their lifespan. When not in use, store your excavator in a dry, shaded area to protect the tracks from prolonged exposure to sunlight and extreme temperatures. UV rays and heat can degrade the rubber, leading to cracks and reduced durability. If indoor storage is unavailable, consider using a protective cover to shield the tracks.
Avoid operating your excavator with rubber tracks on sharp or abrasive surfaces whenever possible. These surfaces can cause cuts and punctures, reducing the tracks’ lifespan. When transitioning between terrains, slow down to minimize stress on the tracks. Additionally, avoid making sharp turns or sudden stops, as these actions can accelerate wear.
By following these best practices, you can maximize the performance and durability of your rubber digger tracks. Proper care and mindful usage ensure your tracks remain reliable and efficient for years to come.
Expert Insights and Future Trends in Rubber Excavator Tracks
Expert Recommendations for Buying Rubber Tracks
Experts emphasize the importance of aligning your purchase with your specific operational needs. When selecting rubber excavator tracks, you should prioritize compatibility with your machine’s specifications. Always verify the track width, pitch, and number of links to ensure a proper fit. Ignoring these details can lead to performance issues and unnecessary wear.
Durability is another critical factor. Experts recommend choosing tracks made from high-quality rubber compounds reinforced with steel cores. These materials withstand challenging conditions and extend the lifespan of your excavator with rubber tracks. Tracks with anti-cracking technology or enhanced bonding between layers are particularly reliable.
You should also consider the terrain and application. For soft or muddy ground, tracks with deeper treads provide better traction. Non-marking tracks work best for delicate surfaces like indoor flooring or asphalt. Heavy-duty tracks are ideal for rugged environments where durability is essential.
Experts advise against choosing tracks based solely on price. While budget constraints are important, opting for the cheapest option often results in higher long-term costs due to frequent replacements. Instead, focus on value. High-quality tracks may have a higher upfront cost, but they reduce downtime and maintenance expenses.
Finally, consult trusted suppliers or manufacturers. Reputable brands often provide warranties and customer support, ensuring peace of mind. Some suppliers even offer expert guidance to help you select the best rubber digger tracks for your needs. By following these recommendations, you can make an informed decision and maximize the efficiency of your equipment.
Emerging Trends in Rubber Track Technology
The rubber track industry continues to evolve, introducing innovations that enhance performance and sustainability. One notable trend is the development of eco-friendly rubber compounds. Manufacturers are now creating tracks using materials that reduce environmental impact without compromising durability. These advancements appeal to businesses aiming to adopt greener practices.
Another emerging trend is the integration of smart technology. Some excavator tracks now feature embedded sensors that monitor wear and performance. These sensors provide real-time data, helping you identify potential issues before they escalate. This proactive approach minimizes downtime and extends the life of your tracks.
Improved tread designs are also gaining attention. Modern tracks feature advanced patterns that optimize traction on various terrains. Multi-bar and hybrid tread designs offer versatility, making them suitable for both soft and hard surfaces. These innovations enhance the adaptability of excavators with rubber tracks, allowing operators to tackle diverse projects with ease.
Additionally, manufacturers are focusing on lightweight yet durable materials. Lighter tracks reduce the overall weight of the machine, improving fuel efficiency and reducing operational costs. Despite being lighter, these tracks maintain the strength needed for demanding applications.
Lastly, the industry is exploring modular track systems. These systems allow you to replace individual sections of a track instead of the entire unit. This approach reduces waste and lowers replacement costs, making it a cost-effective solution for maintaining rubber digger tracks.
Staying informed about these trends ensures you remain ahead in the industry. By adopting innovative technologies and materials, you can enhance your machine’s performance while contributing to sustainable practices.
Choosing the right digger tracks is essential for maximizing your machine’s performance and saving costs. Tracks that match your machine’s specifications, terrain, and workload ensure efficiency and durability. Proper maintenance further extends their lifespan, reducing downtime and expenses.
You should consult experts to make informed decisions and explore the latest trends in rubber track technology. These innovations can enhance your equipment’s capabilities and sustainability. Take the next step by researching trusted brands or reaching out to reliable suppliers. Investing in quality tracks today ensures smoother operations and long-term success for your projects.
Post time: Nov-26-2024