Excavator tracks
Excavator rubber tracks are an important part of excavator equipment, providing traction, stability and durability in a variety of operating conditions. Made from premium rubber compound and reinforced with an internal metal core for strength and flexibility. Featuring a tread pattern design optimized for all terrains while minimizing ground disturbance. Available in different widths and lengths to suit various excavator models.
Excavator rubber tracks are used in construction, landscaping, demolition and agriculture. Suitable for working on a variety of surfaces including dirt, gravel, rocks and pavement. Ideal for confined spaces and sensitive jobsites where traditional rails can cause damage. Compared with steel rails, the maneuverability is enhanced, the ground pressure is reduced, and the disturbance to the site is minimized. Improves operator comfort and reduces vibration and noise levels during operation. Reduce maintenance costs and reduce the risk of damaging paved surfaces. Increases flotation and traction in soft or uneven terrain, improving overall machine performance. Evenly distributes the weight of the machine, reducing ground pressure and minimizing ground disturbance. Provides excellent grip and control, especially when working on sloping or challenging surfaces. Protects delicate surfaces such as asphalt, lawns and sidewalks from damage during operations.
In summary, excavator tracks offer superior traction, reduced ground disturbance, and versatility on a variety of terrains, making them essential for efficient, low-impact excavation and construction operations.
Advantages of our products
Changzhou Hutai Rubber Track Co., Ltd. is a company specializing in the manufacturing and sales of rubber excavator tracks and rubber track blocks. We have more than 8 years of manufacturing experience in this industry and have great confidence in product production and quality assurance. Our products mainly have other advantages:
Less damage per round
Rubber tracks furrow soft ground less than steel tracks from wheel products and damage the road less than steel tracks. Rubber tracks may protect grass, asphalt, and other delicate surfaces while minimizing harm to the ground because of the rubber's mild and elastic nature.
Small vibration and low noise
For equipment operating in congested areas, mini excavator tracks products are less noisy than steel tracks, which is an advantage. Compared to steel tracks, rubber tracks produce less noise and less vibration during operation. This helps improve the operating environment and reduces disruption to surrounding residents and workers.
High speed operation
Rubber excavator tracks allow the machine to travel at higher speeds than steel tracks. Rubber tracks have good elasticity and flexibility, so they can provide faster movement speed to a certain extent. This may lead to efficiency improvements on some construction sites.
Wear resistance and anti-aging
Superior mini digger tracks can withstand a variety of challenging operating situations and still retain their long-term stability and durability thanks to their strong wear resistance and anti-aging characteristics.
Low ground pressure
The ground pressure of machinery fitted with rubber tracks can be relatively low, about 0.14-2.30 kg/CMM, which is the major reason for its use on wet and soft terrain.
Excellent traction
The excavator can navigate rough terrain more easily because of its improved traction, which enables it to draw twice as much weight as a wheeled vehicle of the same size.
How to maintain excavator tracks?
1. Upkeep and cleaning: Excavator rubber tracks should be cleaned frequently, especially after use, to get rid of accumulated sand, dirt, and other debris. Use a water-filled flushing device or a high-pressure water cannon to clean the tracks, paying particular attention to the grooves and other small areas. When cleaning, make sure everything dries completely.
2. Lubrication: The digger tracks's links, gear trains, and other moving parts should all be lubricated on a regular basis. Chain and gear train flexibility are preserved and wear is decreased by using the appropriate lubricant. However, do not let oil contaminate the excavator's rubber treads, especially when refueling or using oil to lube the drive chain.
3. Adjust the tension: Make sure the rubber track's tension satisfies the manufacturer's specifications by checking it on a regular basis. Rubber tracks must be routinely adjusted since they will interfere with the excavator's ability to operate normally if they are too tight or too loose.
4. Prevent damage: Steer clear of hard or pointy items when driving because they can quickly scratch the rubber track's surface.
5. Regular inspection: Look for wear, cracks, and other damage indicators on the rubber track surface on a regular basis. When issues are found, have them fixed or replaced right away. Verify that every auxiliary part in the crawler track is operating as intended. They should be replaced as soon as possible if they are very worn out. This is the fundamental requirement for the crawler track to function normally.
6. Storage and use: Try not to leave the excavator out in the sun or in an area with high temperatures for an extended period of time. The life of the rubber tracks can typically be extended by taking preventative steps, such as covering the tracks with plastic sheets.
How to produce?
Prepare the raw materials: The rubber and reinforcing materials that will be used to make the main construction of the rubber digger tracks, such as natural rubber, styrene-butadiene rubber, Kevlar fiber, metal, and steel cable, must first be prepared.
Compounding is the process of combining rubber with additional ingredients in predetermined ratios to create a rubber mixture. To guarantee even mixing, this procedure is often carried out in a rubber compounding machine. (To create a rubber pads, a certain ratio of natural and SBR rubber is combined.)
Coating: Coating reinforcements with a rubber compound, typically in a continuous production line. Rubber excavator tracks can have their strength and durability increased by adding reinforcement material, which can be steel mesh or fiber.
Forming: The structure and form of the digger tracks are created by passing rubber-coated reinforcement through a forming die. The material-filled mold will be supplied into a sizable production apparatus, which will press all of the materials together using high-temperature and high-capacity presses.
Vulcanization: In order for the rubber material to cross-link at high temperatures and acquire the necessary physical qualities, the molded mini excavator rubber tracks must be vulcanized.
Inspection and trimming: To make sure the quality satisfies requirements, vulcanized excavator rubber tracks must be inspected. It might be necessary to do some more trimming and edging to make sure the rubber tracks measure and seem as intended.
Packaging and leaving the factory: Finally, the excavator tracks that meet the requirements will be packaged and prepared to leave the factory for installation on equipment such as excavators.
After-sales service:
(1) All our rubber tracks have serial numbers, and we can track the product date based on the serial number. Typically 1 year factory warranty from date of production, or 1200 operating hours.
(2) Large Inventory - We can provide you with the replacement tracks you need when you need them; so you don't have to worry about downtime while waiting for parts to arrive.
(3) Fast Shipping or Pickup - Our replacement tracks ship the same day you order; or if you're local, you can pick them up directly from us.
(4) Experts Available - Our highly trained, experienced team members know your equipment and will help you find the right route.
(5) If you cannot find the excavator rubber track size printed on the track, please inform us of the crackdown information:
A. The make, model and year of the vehicle;
B. Rubber Track Dimensions = Width (E) x Pitch x Number of Links (described below).

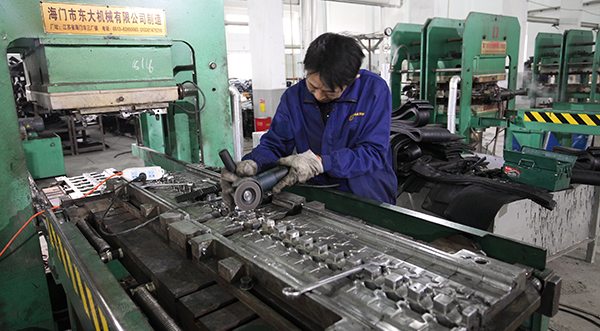


Why choose us?
1. 8 years of manufacturing experience.
2. 24-hour online after-sales service.
3. Currently we have 10 vulcanization workers, 2 quality management personnel, 5 sales personnel, 3 management personnel, 3 technical personnel, and 5 warehouse management and cabinet loading personnel.
4. The company has established a quality management system in accordance with ISO9001:2015 international standards.
5. We can produce 12-15 20-foot containers of rubber tracks per month.
6. We have strong technical strength and complete testing methods to monitor the entire process from raw materials to finished products leaving the factory. Complete testing equipment, a sound quality assurance system and scientific management methods are the guarantee of the quality of our company's products.

